It’s a problem we see more often than we should – inconsistent results from factories that prioritize cost by cutting corners. The levels looked fine in the box, but spirit vials were often poorly calibrated and the anodization often suffered discoloration.
Problem: Identified
Solution: Applied
• First, a more organized SOP was produced, with more emphasis on quality checking, calibrating the surfaces and higher precision calibration equipment.
• For the anodization process, new equipment was introduced performing ultrasound cleaning along with a stage of QC before the chemical etch process to eliminate flashing as well as clean off any residues and watch for surface irregularities.
• Consistency was improved to the point of 100% viable product per finished batch. Unusable metal samples were discarded before reaching the anodization process and unusable spirit vials were also identified before installation.
Note: The identity of the client is obscured for the purposes of upholding our NDA.
PROBLEM: SOLVED.
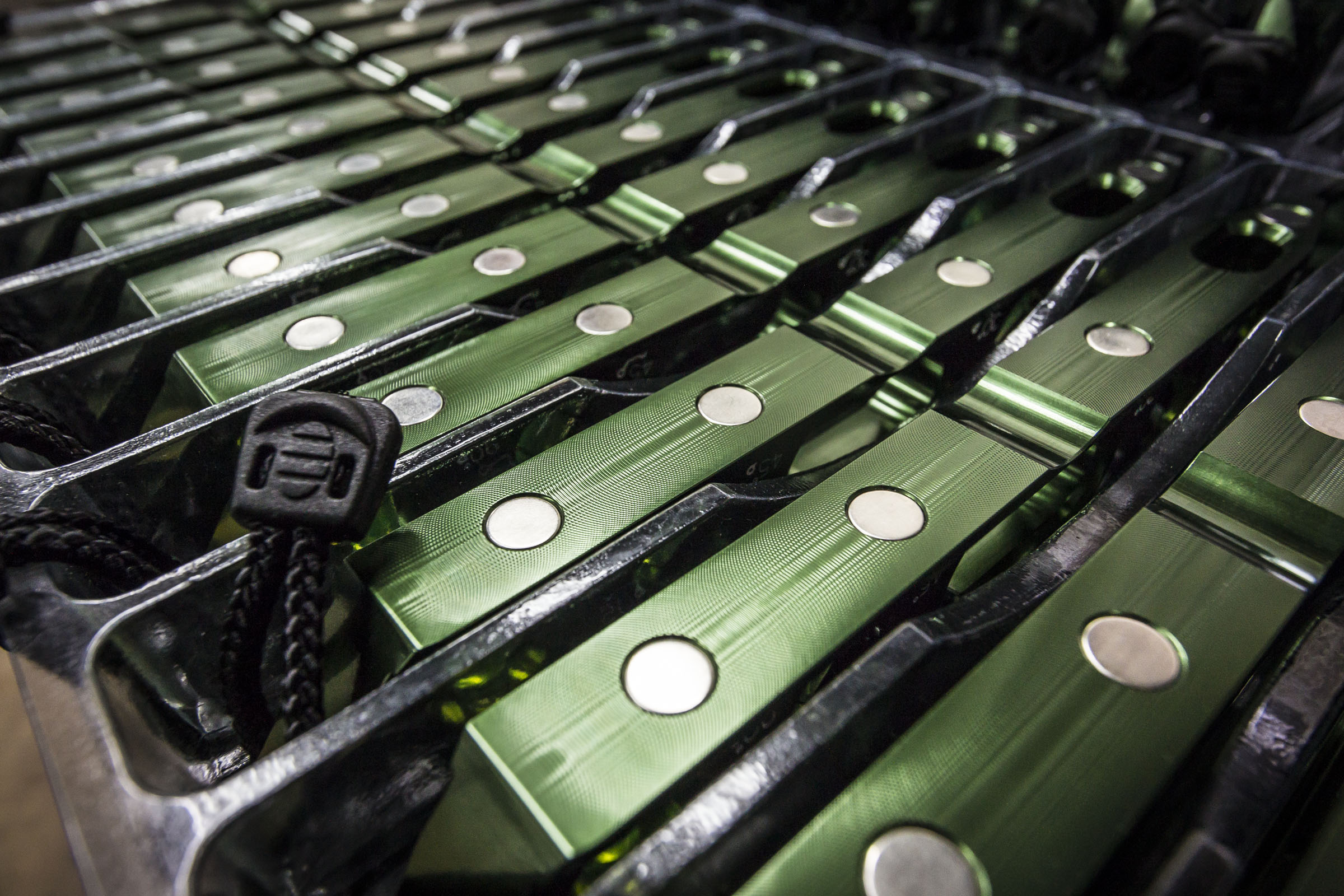
The difference
experience makes
A network of factories come together to produce items like this, from foundries for handling aluminum stock, milling and drilling factories, polishing facilities, anodizing and chemical processing factories and multiple stages of QC.
- Decades of experience from specialists in each field
- Practical solutions for real-world problems
- Consistency in applied solutions
- Adaptable production line
Get in touch
Tell us a little bit about your project, your company, your history and any obstacles you'd like to work on and we'll be in contact with you ASAP.
If you would like us to work under an NDA, we are happy to accommodate this.